Kanban University and Scrum Alliance Partner to Offer Dual-Credential Course: "Scrum Better with Kanban"
Kanban University, the world’s foremost authority on the Kanban Method, is partnering with Scrum Alliance®, a global leader in agile education and certification, to deliver a first-of-its-kind learning experience: Scrum Better with Kanban. This course offers professionals a structured way to optimize their Scrum practice by incorporating the clarity, focus, and flow of Kanban while earning two respected credentials from two of the world’s top iterative delivery and flow-based work organizations.
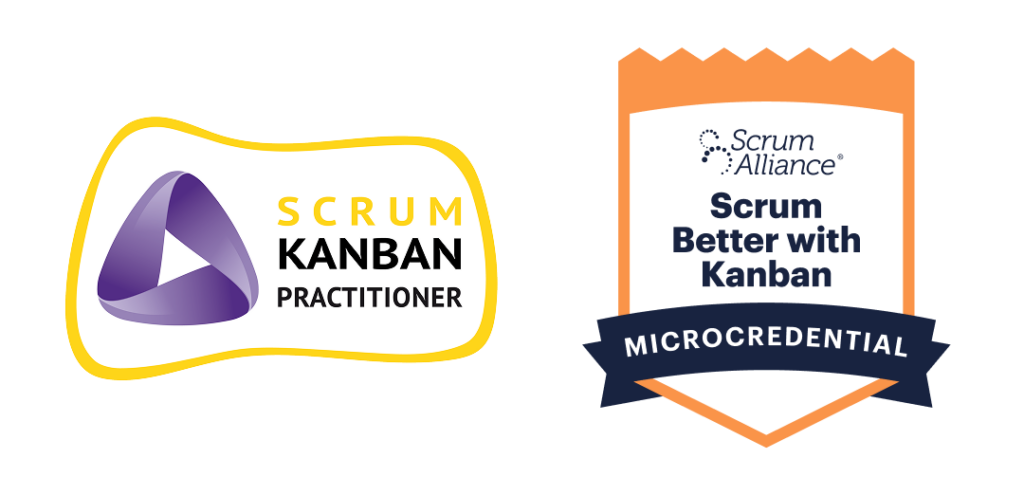
This partnership brings together two schools of thought that have shaped how modern teams work. Scrum Alliance and Kanban University have long served complementary roles in the agile ecosystem. By joining forces, they’re signaling a pivotal shift, one that acknowledges the evolving needs of agile practitioners and the value of blended approaches.
“Visualizing work, whether it be tasks, processes, or broader initiatives, is essential to helping teams stay aligned and deliver value,” said Scrum Alliance Chief Executive Officer, Tristan Boutros. “This partnership with Kanban University helps professionals bring clarity to their work, improve flow, and adapt their priorities with greater confidence. By combining the spirit of the Kanban Method with the cadence of scrum, we aim to support all product and service teams as they navigate complexity in today’s ever-changing economy, with greater ease and effectiveness.“
This course is designed to meet the growing demand for flexible and pragmatic approaches to agility in the workplace. Participants will learn how to:
- Visualize work and make bottlenecks easier to identify and address
- Limit Work in Progress to improve value delivery
- Create effective feedback loops that enhance team alignment
- Apply evidence-based improvement practices to achieve meaningful change
“This partnership reflects what we see every day: teams want practical ways to deliver better and faster while creating real, lasting change,” said Kanban University President, Stephanie Dziad. “By bringing together the strengths of scrum and kanban, we’re giving professionals the clarity and confidence to make meaningful improvements in how their teams work.“
With an emphasis on practical application over theoretical instruction, learners leave the course with tools and insights they can use immediately, whether they’re scrum masters, team leads, product managers, or part of a broader agile initiative.

Scrum Better with Kanban Course details:
Format: Live online and led by an experienced, dual-credentialed trainers
Duration: 8 hours
Prerequisites: None
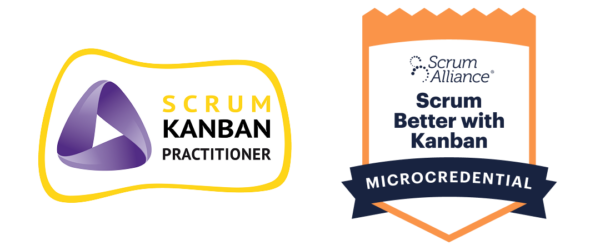
The combined strength of Scrum Alliance and Kanban University sends a clear message: Agile practices are built to evolve in response to real-world challenges and your team’s unique needs. Scrum Better with Kanban represents the more adaptive, integrated approaches that reflect the way teams truly work today.
To learn more or register, visit the Scrum Alliance website or search for courses now.
About Scrum Alliance
As the first not-for-profit focused on agile education and professional credentialing, Scrum Alliance continues to advance its position of Agile for Anyone™ by equipping professionals and their organizations with the education, skills, and community needed to succeed in today’s ever-evolving workplaces.
About Kanban University
As the global leader of the Kanban Method, Kanban University provides high-quality professional education and credentials to improve how organizations deliver value. Through its worldwide community, Kanban University empowers professionals to achieve greater visibility, continuous improvement, and flow while leading evolutionary change in their teams and scale across multiple connected systems to the whole organization.