KANBAN METHOD FINE-TUNES WARRANTY
CLAIMS SYSTEM AT VOLVO GROUP
Volvo Group, a leading global transportation and construction equipment provider, originally took a traditional approach to maintaining its online system for processing warranty claims submitted by owners of commercial trucks and buses. When warranty claims spiked, the system’s IT team would struggled to respond, resulting in unhappy customers who complained of losing money. Introducing Kanban brought clarity to the team’s workflow and increased efficiency, accelerating customer delight.
SERVICE DELIVERY COMMITMENT
The Kanban Method allows you to manage your capabilities so that you can make promises that you can keep. With Kanban you can effectively measure your service, judge the impact of changes you introduce, and use data to effectively predict your delivery capabilities.
The Challenge
SWC, Volvo’s warranty claims system for heavy-duty vehicles, is a web application that sources individual vehicle information and warranty claims and shares that information with other Volvo systems to process claims. SWC was introduced for Volvo trucks and buses and completely replaced the. previous warranty claims system. The SWC team consists of a business unit as well as an IT team that provides system support and develops new functionality that adapts to Volvo’s growing global business.
SWC’s development style had always followed the traditional approach to software development, which sorts development into batched sequential phases, making each phase dependent on the deliverables of the previous one. This had been the IT team’s approach from the start, and it was initially effective, but increased demand from Volvo’s global expansion began to add stress to the system.
The IT team was in crisis. New, complex projects were being initiated without clear direction from the business side, leading to confusion, delays, and criticism. Volvo had moved to consolidate many of its internal systems in an effort to improve workload efficiency. The IT team was overwhelmed, and communication breakdowns hindered progress. Eventually, SWC leadership recognized the need for change and began looking for ways to cope with increased demand.
The Solution
SWC leadership sought a solution that wouldn’t dramatically change the way its team members worked. There was too much ongoing work and numerous deadlines to meet. As it happens, another team within Volvo Group had adopted the Kanban practice of visualizing work in progress, which had helped them improve management decision-making and delivery of services. This other team hadn’t changed the way they worked; they simply made it more transparent. So, SWC’s IT team decided to give Kanban a try, too.
The team began by creating digital Kanban boards focused on project work, maintenance, support, and high-priority tasks. The Kanban boards provided transparency into the team’s workflow, visualizing task progress and revealing bottlenecks. Some team members were uncertain it would work, but the digital Kanban system, SwiftKanban, facilitated a smooth transition to a new way of working. Separate boards were created for large projects and daily standup meetings were introduced to enhance communication.
VISUAL MODELS
Knowledge work is largely intangible. Kanban uses visual models such as boards and metrics to “unhide” work in progress. This creates visibility into status and a single point of truth for collaboration.
The Transformation
Introducing Kanban helped the IT team identify several key reasons why deliverables were often delayed, especially in SWC’s big projects. Put simply, requirements were unmanageable and unclear. Addressing this issue prompted helpful conversations between the SWC team’s IT and business units.
Meanwhile, the IT team began looking at the Kanban data. The data provided by SwiftKanban especially helped diagnose shortcomings in IT’s delivery rate, lead time, and employee work behavior. Kanban had acted as an x-ray and opened everyone’s eyes to “the ugly truth,” as one employee put it.
By October, SWC IT saw the first release since the beginning of the year. However, it revealed numerous defects, prompting the creation of a dedicated Kanban board for fixing defects. This experience highlighted the importance of task size, clear requirements, and the detrimental effects of multitasking. The team learned that small, focused tasks, combined with self-organization, led to successful deliveries.
Adapting and Sustaining Change
The IT team experienced a change of mindset: Work became part of a common goal — a good and timely release — not just another phase in the business model. The team would often finish a task before starting a new one, and team members established individual work-in-progress (WIP) limits and avoided multitasking. The team further progressed by incorporating other Kanban principles such as managing the product backlog, systematizing WIP limits, and settling on an explicit “definition of done.”
As the team became more comfortable with Kanban, their Kanban boards became simpler, making it easier for team members to understand the workflow, collaborate, and continue to improve. SWC has shown that they can improve delivery, providing a genuine business benefit for Volvo and its customers.
The SWC team’s journey showcases the transformative power of the Kanban Method in addressing complex challenges within large IT teams. By promoting transparency, limiting WIP, and emphasizing small, focused tasks, Kanban streamlined delivery and made it easier for the IT team to adapt and evolve in Volvo’s rapidly changing business environment.
EVOLUTIONARY, NOT REVOLUTIONARY
“Start with what you do now” and improve upon it! We respect the existing business, its processes, and its capabilities. We seek to improve through safe-to-try evolutionary means. No reorganizations. No one gets a new job title, role, or responsibilities. We respect the identity of the organization, its employees, and groups.
Interested in staying up to date on the latest Kanban News and Resources? Sign up for our mailing list today!
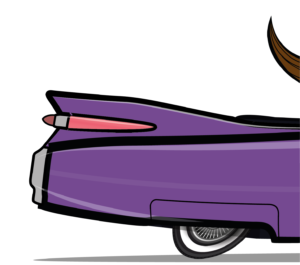