A STORY OF CORPORATE RESILIENCE AND INNOVATION
BLIZZARD SPORT WINS WITH THE KANBAN METHOD
Austrian sports equipment company Blizzard Sport, founded in 1945, was acquired by Italy’s Tecnica Group in 2006 due to an unusually warm winter in the Alps that year, which piled up unsold inventory and threatened its solvency. Blizzard’s acquisition marked a key turning point for the company, leading to a transformative journey that saw the introduction of lean manufacturing principles and the Kanban Method, which shifted Blizzard’s culture toward continuous improvement and employee empowerment.
Kanban is a powerful management approach that, unlike other solutions, doesn’t prescribe a fixed set of behaviors or actions. Instead, it encourages continuous improvement by enabling teams to start where they are and improve from there using techniques such as visualizing workflow and limiting work in progress. The Kanban Method scales across an entire organization by introducing it into one service or product line at a time.
Background
Skiing holds profound significance in Austria, not just as a sport but as a source of national pride. Blizzard, based in Mittersill, became famous in 1954 for being the first manufacturer to mass produce polyethylene ski bases1.1 In 1957, it introduced metal and fiberglass materials into its products, further burnishing its reputation as an innovator. It soon became the cornerstone of the local economy, employing hundreds of people and supporting numerous suppliers.
The acquisition by Tecnica in the wake of the warm winter of 2006-2007 created dramatic changes at Blizzard’s factory. Not only was it mass-producing Blizzard skis, but now it was also producing skis and ski boots developed by Nordica, an Italian manufacturer of winter sports products owned by Tecnica Group.
The Challenge
Consolidating production introduced new challenges in the traditional ski production cycle, marked by overproduction, long lead times, and inefficient forecasting. The traditional cycle of ski production begins a year before the skis are on the market, meaning skis for the 2006–2007 winter season would have begun production in November of 2005.
Tecnica’s initial focus on cost reduction through an enterprise resource planning system yielded limited benefits. Blizzard succeeded in making skis cheaper but failed to produce enough skis to meet demand. The turning point came when consultants from Porsche Consulting introduced lean manufacturing principles, derived from the automobile industry, which aims to eliminate waste and enhance efficiency.
The Turnaround
In 2011, Blizzard embraced lean manufacturing, with a focus on transparency, waste reduction, and continuous improvement. Waste, defined as activities that don’t directly create value for customers, is often much more widespread than simply incurring extra costs. That turned out to be true at Blizzard.
The introduction of Kanban, including its visual management approach, also played a pivotal role in Blizzard’s turnaround. Employing a physical Kanban board revolutionized the production process by creating a transparent workflow and empowering employees to evolve their individual work processes.
KEY ELEMENTS OF THE KANBAN METHOD
The combination of process transparency and workflow visualization is a common theme in the Kanban Method. These elements empower individual team members to make decisions and manage risks on their own. Management eventually comes to trust the system because they understand the process is made up of policies explicitly designed to manage risk and deliver customer expectations.
Kanban’s Expansion into Information Technology
While improvements were becoming evident on the factory floor, Blizzard’s information technology (IT) team began facing fresh challenges of its own. The IT team was bogged down with increased requests, a lack of prioritization, and delays in service delivery. Seeking a solution, and motivated by the company’s embrace of lean manufacturing and Kanban, the team’s chief information officer introduced the Kanban Method for IT.
The team introduced a physical Kanban board with columns such as “Next in Line,” “Build,” and “Test.” This provided visibility into the team’s ongoing tasks and streamlined communication with internal clients. The team set work-in-progress (WIP) limits, which reduced multitasking and enhanced task completion.
WIP, or work in progress, describes the number of work items in progress at a given time. Focusing more on the flow of work and less on worker utilization is central to how Kanban works. When teams employ Kanban, they limit WIP to balance worker utilization and the overall flow of work.
Success and Recognition
Introducing Kanban within manufacturing and IT proved successful. Blizzard’s production process became more responsive and significantly reduced lead times. Evolutionary change became ingrained in Blizzard’s culture, leading to better wages for employees and enhanced overall efficiency. The cultural shift also influenced other departments within the company, and it even reached Tecnica’s headquarters in Italy! Introducing lean principles and Kanban also led to Blizzard’s CIO receiving the 2013 CIO Award for Best IT Manager in Austria. He would go on to lead business processes at Tecnica.
Conclusion
Blizzard Sport’s journey from a crisis-ridden manufacturer to a lean and resilient organization showcases the transformative power of lean manufacturing principles and the Kanban Method. The company’s success story can serve as a source of inspiration for other industries facing similar challenges, emphasizing the importance of adaptability, transparency, and a culture of continuous improvement.
EVOLUTIONARY, NOT REVOLUTIONARY
“Start with what you do now” and improve upon it! We respect the existing business, its processes, and its capabilities. We seek to improve through safe-to-try evolutionary means. No reorganizations. No one gets a new job title, role, or responsibilities. We respect the identity of the organization, its employees, and groups.
Interested in staying up to date on the latest Kanban News and Resources? Sign up for our mailing list today!
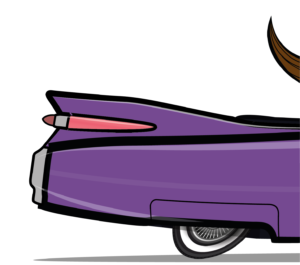